Coega mill confident SA can be continent's green-steel hub
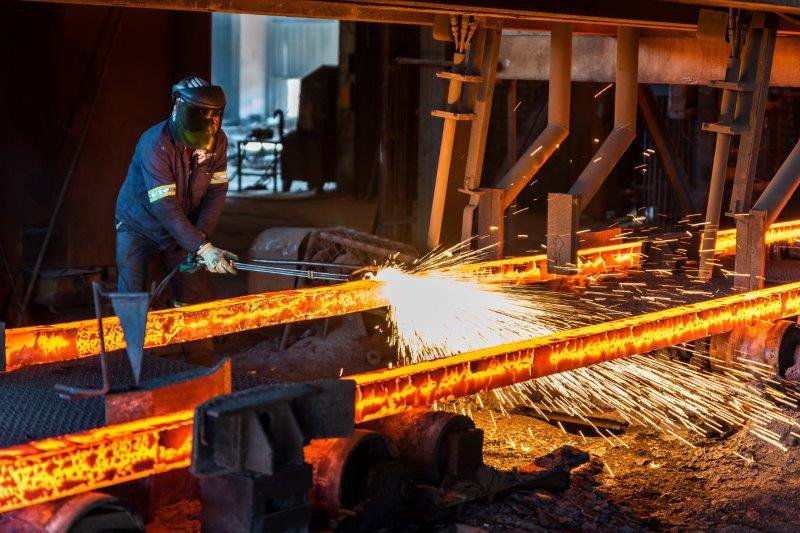
Amit Saini, a director at Eastern Cape-based Coega Steels Pty Ltd, has no doubt that South Africa can be Africa’s green-steel hub. Pictured are steel billets produced in the Gqeberha mini mill’s induction furnace which, along with electric arc furnaces, h
South Africa’s steel production output last year reflects the significant contribution being made by secondary-steel producers to the economy and efforts to curb carbon emissions.
While producers using traditional coal-fired blast furnaces produced 2.59-million tonnes of steel in 2024, the so-called mini mills, where steel is made from scrap metal, yielded approximately 2.11-million in the same 12-month period.
While the respective outputs are relatively on par, the biggest differentiator is that mini mills emit roughly four to five times less carbon than primary steel producers.
Amit Saini, one of the directors of Eastern Cape-based mini mill Coega Steels Pty Ltd, explained that the manufacture of so-called “green steel” had gained greater prominence as industries embraced sustainable practices to mitigate environmental impacts.
“This shift is driven by increasing regulatory pressures, consumer demand for eco-friendly products and international commitments to reduce carbon emissions under pacts such as the legally-binding Paris Agreement on climate change,” Saini said.
“Steelmaking through scrap recycling is the leading and foremost method of green steel production. Recycling scrap metal significantly cuts carbon emissions compared to traditional methods.”
India has already established itself as a global leader in the green-steel sector.
In terms of new guidelines released by the South Asian nation, steel with a carbon footprint of less than 1.6 tonnes of carbon dioxide equivalent (CO2e) per tonne of finished steel (tfs) is defined as five-star green steel.
That with emissions of 1.6 to 2.0 tonnes is rated four-star while 2.0 to 2.2 is three-star.
Saini said this landmark policy underscored the importance of setting clear guidelines to promote green steel. The United States and many European countries have also implemented stringent green-steel standards.
“These developments highlight the competitive advantage of green steel, which is sold at a premium in international markets due to its lower environmental impact,” Saini said.
Aside from the scrap recycling aspect, the significantly-lower carbon footprint is also attributable to the type of furnace being used – whether electric arc (EAFs) or induction, the latter of which is operational at Coega Steels.
The Gqeberha mini mill’s furnaces, which are only able to process ferrous material containing iron, melt metals by way of electromagnetic induction.
Blast furnaces, on the other hand, producesteel from iron ore, coke and limestone.
Saini said it was increasingly clear that South Africa was perfectly placed to lead the “green-steel revolution” in Africa, given its strategic position in regional and global markets.
“We have the biggest base of mineral resources compared to other African countries. These carry an estimated value of US$2.5-trillion (R44-trillion).
“While coal is widely used domestically (nearly 75 per cent of its mined volume is used for, among others, electricity, chemical and liquid fuel production) and the balance exported, the story is different for iron ore.”
He said more than 90 per cent of iron ore mined in SA was being exported due to limited domestic beneficiation (enhancing the economic value of raw materials) and constraints in the primary steel sector’s manufacturing capacity.
Accordingly, Saini said, SA should expand domestic beneficiation policies to include iron ore and coal, thereby enhancing their local value addition and reducing the reliance on exports.
To maximise the country’s potential as a continental leader, it is imperative to revitalise the primary steel sector’s manufacturing capacity.
“This should be done through targeted investments and policy incentives to develop mechanisms that will ensure cost-effective procurement of raw materials for domestic steel producers, therefore enhancing competitiveness.
“By using iron ore to produce Direct Reduced Iron (DRI), we can alleviate potential scrap metal shortages in the domestic market in the future,” Saini explained.
“It is a viable substitute for scrap and aligns well with the future of steel production in the country, particularly given the increasing adoption of EAFs over the next few years.”
DRI-based steel production offers various benefits.
For one, it is less harmful to the environment. For another, DRI can ensure sustainable growth in steel production should SA reach a saturation point in scrap availability.
Saini said while the country currently lacked a merchant/trading DRI plant, affordable raw materials would become accessible to existing producers, thereby encouraging new production capacity, should iron ore and coal beneficiation policies be promulgated.
He added since South Africa had received more than US$4-billion (R73-billion) in funding from bilateral and multilateral sources to help reduce carbon emissions, there was an obligation to implement actionable plans that aligned with global climate goals.
“Promoting green-steel production is a practical and impactful way to meet these commitments.”
Author: Coetzee Gouws, Full Stop Communication